The last section of the new Genoa bridge’s deck was put in place on April 28, marked by a national ceremony attended by Prime Minister Giuseppe Conte. Now all eyes turn towards July, when this replacement for the collapsed Morandi bridge should be completed and handed over to the city of Genoa.
The piers are now finished, and so is the deck, which has reached its final length of 1,067 metres (3,500 feet). The worksite 40 metres (131 feet) in the sky is about to shut.
“We still have a few more days of holding our breath,” explains Stefano Mosconi, Salini Impregilo’s engineer who manages the bridge site. “If the construction of the new bridge in Genoa were a 100-metre race, we would now be in the final sprint.”
This last step involves completing all the installations hidden inside the deck, as well as finishing the road that will be used by vehicles once the bridge is inaugurated. Salini Impregilo, which is carrying out the work with Fincantieri, is using the same organisational model that has made it possible to pull out all the stops to deliver the bridge in such a short time.
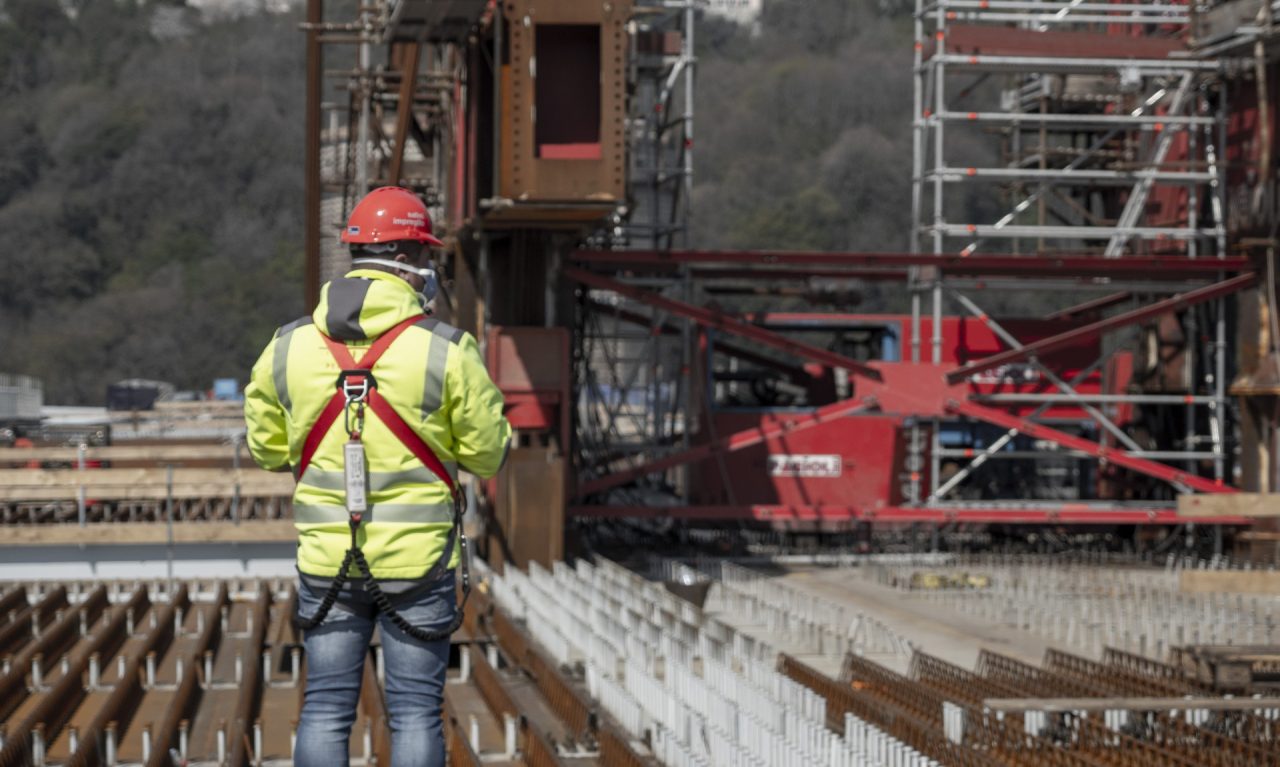
Genoa Bridge construction: the positioning of the bridge
The completion of all the decks, some of which were lifted into place without being fully equipped because they would have been too heavy, means the men working on the site can now lay the bridge on the final supports positioned at the top of the piers.
The bridge’s final position will therefore be 25 centimetres (11 inches) lower than the current one. This positioning is a complex operation that also involves the bridge being thermally centred. Only after the large span has been moved in its final position will it be possible to lay the reinforced concrete, a casting that will be 21 centimetres (8.2 inches) thick.
“To lay the reinforced concrete will take about ten days of work, 24 hours a day,” explains Mosconi. “This will allow us to create what we call the ‘back’ of the bridge, where the cars will run. This is the most visible part of the infrastructure, and will finally allow the Genoese to use this beautiful bridge.”
This phase of the work will be particularly complex because it calls for hundreds of workers, employed at the same time on several fronts, while the site complies with the strictest safety measures to protect people from the risk of Covid-19 contagion.
Body temperature is measured by thermo scanners at all entrances to the yard; hand disinfectant has been distributed to all; social distancing is followed to the letter, and of course the working environment and all common areas are frequently cleaned and sanitized. These measures allow work at the yard to continue.
Voices from the Bridge - The podcast series dedicated to the new Genoa Bridge
Installing the technology
This outdoor work will go hand in hand with the completion of the installations inside the deck, in order to give architect Renzo Piano’s bridge a clean, sleek look.
The decks will hide all sorts of high-tech features: channels for disposal and treatment of rainwater, air dehumidification, sensors that monitor the tightness of the structure, and robots that manage maintenance and clean the photovoltaic panels.
“This is not be accident, it is the result of a request by architect Renzo Piano himself: to hide all the management systems in order to give Genoa and travelers an infrastructure that is unique for its beauty,” explains Francesco Poma, engineer at Salini Impregilo and project manager at PerGeova, the joint venture building the bridge.
These hidden compartments in the decks house two kinds of robots: washing robots, in charge of cleaning the solar panels and the external surface of the deck; and inspection robots, particularly innovative machines that will run on rails along the entire length of the bridge, monitoring its conditions. Each inspection cycle of these robots lasts 15 hours, during which the machine is able to take 15,000 images of the structure and report any change in status to the operations centre.
Finishing the Genoa bridge
Once the concrete has been laid on the deck, attention turns to the so-called dressing of the bridge. Glass panels will be installed beginning from the side and central platforms. These panels will be 2.5 metres (8.2 feet) high in order to meet two requirements: safety (the panels have been tested at the Milan Polytechnic to withstand the strong winds of the Polcevera valley) and aesthetic beauty.
“In addition to the glass, we will assemble the photovoltaic panels, which will provide nearly the entire energy supply, starting from the power needed to operate the dehumidification system inside the decks,” said Mosconi. “We will also continue work on laying the drainage channels, cable channels, the waterproofing sheath, the lateral and central safety barriers, and lastly, the paving. This calls for a very tight organisation of almost 40 teams at work simultaneously, and over 150 people including workers and technicians who need to be coordinated like orchestra musicians, to complete the dressing of the bridge in record time and in complete safety.”
The last step before the final tests will be to install the 22 light posts designed for a spectacular illumination of the new bridge. Each of these posts 28 metres (91 feet) high — more than a five-story building — and the tapered shape recalls a ship’s mast. A ship suspended in across the valley of the Polcevera.