The Brenner Base Tunnel is setting several milestones. It is the longest railway tunnel in the world; a unique and innovative work that require the use of complex techniques almost exclusive to the worksite; an opportunity to create jobs; an unparalleled supply chain.
This railway tunnel and Innsbruck bypass reach 64 kilometres (39 miles) in length, and will connect Italy’s Fortezza with Innsbruck in Austria, and from there to Munich, adding yet another section to “Europe’s subway,” the network of TEN-T high-speed rail links supported by the European Union and intended to connect the farthest corners of the continent.
The Webuild Group is taking part in the Brenner Base Tunnel’s construction in two lots. The first is the Isarco Scarl Consortium (led by Webuild and including Strabag, Collini Lavori and Consorzio Integra), which is building 5.8 kilometres (3.6 miles) of tunnels starting from Fortezza and travelling under the Isarco river bed for 240 metres (787 feet); the second is covering the last northern section.
Innovation and sustainability in a record-breaking tunnel
Brenner base tunnel: Webuild’s supply chain
Webuild’s commitment to this tunnel beneath the Alps is supported by a substantial supply and subcontractor chain. On Isarco River tunnel alone, we are talking about 918 companies, including suppliers and subcontractors, 97% of which are Italian companies.
The majority of companies come from regions near the construction site: 717 of them are based in Northern Italy, 134 in the Centre and 43 in the South. The Trentino Alto Adige region has the most: 287, or 32.1% of the total, followed by Lombardy.
In general, these companies are leaders in production know-how, specialising in a wide range of sectors. For example, Geo-Inspector, in charge of monitoring temperatures during the soil freezing phase; Stonex, specialised in precision geodetic instrumentation for machine control systems, and pointing and positioning systems in tunnels for drilling; Costruzioni Meccaniche Romane, involved in the study and supply of technology applied to stabilise the soil below the water table and prepare it for excavation.
More than 1,400 people are involved on this site. A few suppliers have developed techniques especially for this job. Clivio, for example, is bringing two new patented techniques to the site; they are used to stabilise the soil by using jet grouting to prevent the injected cement from being washed away by the aquifer in the tunnel.
“If we are near a watercourse, the greatest risk during soil stabilisation is that it gets washed away,” explains engineer Gianluca Vigna, technical director and partner of Clivio srl. “To deal with this, we have created an accelerated stabilising product, the first of our patented techniques for this site.”
This means that the water/cement mixture has much faster setting times thanks to a special dosage, developed by Clivio, of the accelerating products. These travel through pipes parallel to the cement, preventing water from washing the mixture away to where it is not needed.
Like Clivio, CRM is also involved in soil stabilisation activities, in particular in the supply of drilling and jet grouting equipment.
“We have put our experience into practice to provide the best, cutting-edge and most suitable technology in order to achieve the stabilising and waterproofing of the future High-Speed Base Tunnel and allow the subsequent safe advance excavation, preparatory to the final laying of the final lining,” says Luca Gastaldi, CRM Production and Sales Manager.
These essential activities contribute to making this project a jewel of technology in the field of large complex infrastructures.
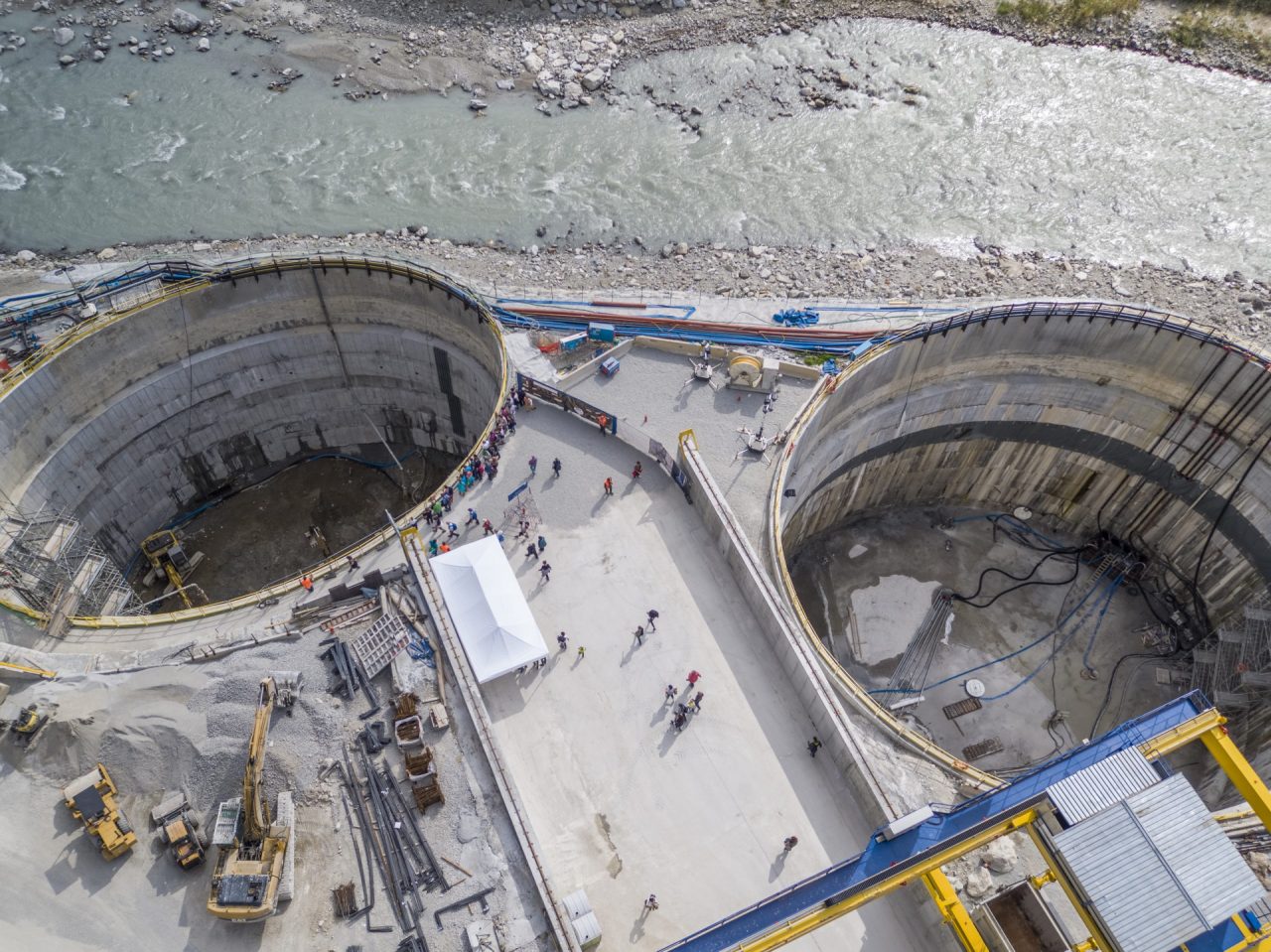
Technical excellence for a record-setting project
The tunnel below the Isarco River is one of the most complex parts of this project. Webuild together with its partner companies is adopting a special freezing technique to carry out this delicate job. The tunnel had its first breakthrough on November 6.
“We are talking about a very complex technique, which starts with drilling the ground under the river and then injections of chemical and cement mixtures necessary to slow down the speed of the water,” explains Webuild engineer Simone Centis, project manager of the site. “Later, liquid nitrogen is passed through the drilled holes, which changes state and becomes gaseous at a temperature of about 196°C (-321°F) below zero. The immediate action of the nitrogen is to freeze the soil surrounding the injection nozzle for about one meter.”
Freezing the ground between the tunnel being excavated and the river above makes the excavation impermeable to water. It also gives resistance and stability to the material around the excavation itself.
In addition to these technical complexities, the Isarco site is also characterized by the high standards of environmental sustainability. The area and the surrounding mountains are protected, and the all site debris is removed from the valley. These are shared goals in the construction of a highly innovative work.
The Brenner Base Tunnel to connect Italy with Europe
The Brenner construction sites are building a high-capacity tunnel where trains will run at 250 km/h, or 155 mph (compared to 130-140 km/h today), transporting both people and goods. This strategic work for trade between Italy and the rest of Europe is part of the TEN-T corridors, and specifically aims to connect Verona and Munich with a single railway axis. In turn, this connection is part of Corridor 1 of the European network.